The Ultimate Guide to Product Packaging Device Repair Work: Keep Your Workflow Running Smoothly
Recognizing the intricacies of product packaging machine fixing is important for maintaining optimal efficiency and lessening disruptions. Routine upkeep not just expands the life of these equipments but likewise addresses usual issues that can hinder performance.
Relevance of Regular Upkeep
Regular maintenance of product packaging devices is vital for guaranteeing ideal efficiency and longevity. By executing a structured upkeep schedule, drivers can determine potential issues before they rise right into substantial problems. This proactive technique not only decreases downtime but also expands the lifespan of the devices, ultimately causing lowered operational costs.
Routine examinations permit the analysis of important elements such as belts, sensors, and seals. Dealing with wear and tear immediately prevents unanticipated failures that can interrupt manufacturing and lead to costly repair services. Additionally, regular maintenance helps guarantee compliance with market requirements and guidelines, fostering a risk-free workplace.
Moreover, upkeep tasks such as cleaning, lubrication, and calibration substantially enhance device effectiveness. Enhanced performance converts to consistent item quality, which is important for preserving consumer satisfaction and brand online reputation. A well-kept product packaging equipment runs at optimum rates and minimizes product waste, adding to overall productivity.
Typical Packaging Machine Issues
Product packaging makers, like any complex equipment, can encounter a variety of common issues that might impede their performance and performance - packaging machine repair. One widespread trouble is irregular sealing, which can result in product putridity and wastefulness if bundles are not appropriately secured. This frequently results from misaligned components or worn sealing aspects
Another regular problem is mechanical jams, which can take place because of international things, worn parts, or incorrect placement. Jams can trigger hold-ups in manufacturing and rise downtime, eventually influencing overall productivity. Additionally, electronic breakdowns, such as failing in sensors or control systems, can interrupt operations and lead to incorrect dimensions or irregular device habits.
In addition, concerns with item feed can additionally emerge, where things may not be provided to the product packaging area regularly, causing disruptions. Wear and tear on belts and rollers can lead to suboptimal efficiency, calling for prompt attention to protect against further damage.
Recognizing these common issues is vital for keeping the honesty of product packaging procedures, making sure that equipment runs smoothly and effectively, which consequently aids in meeting manufacturing targets and keeping product quality.
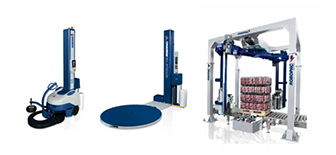
Fixing Techniques
Reliable repairing techniques are crucial for immediately resolving issues that emerge with product packaging devices. An organized technique is essential for determining the origin reason of breakdowns and lessening downtime. Begin by collecting information concerning the symptoms observed; this might consist of unusual noises, functional hold-ups, or error codes displayed on the maker's user interface.
Following, describe the equipment's guidebook for fixing guidelines certain to the version concerned. This resource can offer valuable understandings right into common problems and recommended diagnostic actions. Make use of aesthetic assessments to look for loose connections, worn belts, or misaligned components, as these physical elements frequently contribute to operational failings.
Carry out a process of removal by testing private machine features. For circumstances, if a seal is not creating appropriately, evaluate the securing mechanism and temperature setups to determine if they meet operational specs. File each action taken and the outcomes observed, as this can help in future repairing efforts.
Fixing vs. Substitute Choices
When confronted with devices breakdowns, choosing whether to fix or change a packaging equipment can be a complicated and vital selection. This choice hinges on numerous essential factors, consisting of the age of the machine, the level of the damage, and the predicted influence on functional effectiveness.
To start with, think about the equipment's age. Older makers might require even more frequent repair work, leading to greater collective costs that can surpass the investment in a brand-new device.
Operational downtime is an additional crucial factor to consider. Spending in a brand-new equipment from this source that provides enhanced efficiency and dependability might be extra sensible if repairing the maker will trigger long term hold-ups. Take into consideration the availability of parts; if substitute parts are tough to come by, it might be extra strategic to replace the machine completely.
Inevitably, doing a cost-benefit analysis that consists of both prompt and lasting ramifications will certainly assist in making an informed decision that lines up with your operational objectives and budgetary restrictions. (packaging machine repair)
Preventative Steps for Longevity

Secret preventive steps consist of routine lubrication of moving components, alignment checks, and calibration of controls and sensing units. Developing a cleansing schedule to remove my site particles and impurities from machinery can substantially reduce wear and tear (packaging machine repair). Additionally, keeping an eye on operational parameters such as temperature and vibration can assist spot abnormalities beforehand
Educating team to identify signs of wear or malfunction is one more crucial component of preventive upkeep. Encouraging drivers with the understanding to do fundamental troubleshooting can result in quicker resolutions and lessen functional disturbances.
Documents of upkeep activities, including service documents and assessment searchings for, cultivates accountability and facilitates informed decision-making relating to fixings and substitutes. By focusing on preventive measures, companies can guarantee their packaging makers run at peak performance, inevitably resulting in raised productivity and lowered operational prices.
Verdict
Finally, the reliable repair and maintenance of product packaging makers are critical for maintaining operational performance. Normal upkeep reduces the danger of common issues, such as irregular sealing and try here mechanical jams, while methodical troubleshooting techniques facilitate timely resolution of malfunctions. Furthermore, cautious consideration of repair work versus substitute decisions contributes to cost-efficient management of sources. By carrying out preventative measures, companies can improve equipment long life and guarantee nonstop productivity in product packaging procedures.
Understanding the details of packaging device fixing is crucial for preserving optimum performance and decreasing interruptions.Regular maintenance of product packaging equipments is critical for guaranteeing optimal efficiency and durability.Packaging devices, like any kind of complicated machinery, can come across a variety of typical problems that might prevent their performance and effectiveness. If fixing the machine will create extended hold-ups, spending in a new maker that supplies enhanced performance and dependability could be a lot more sensible.In verdict, the reliable maintenance and fixing of packaging equipments are critical for maintaining operational efficiency.